HomeDefinitionPage 3
Quality VFD's incorporate either an AC Reactor or DC Reactor (choke). Their inclusion in the basic design of the VFD allows the design engineer to maximize the advantages of the choke. Their function is to reduce the current distortion caused by the input stage rectifiers by slowing the rate of change of current, and thus charging the internal capacitor at a slower rate over a longer time.
Sensorless Vector or sensorless feedback has been around awhile. The technology leaders keep coming up with better software and control algorithms to improve performance, which is great. In most applications the VFD far exceeds the motor capabilities. Once you can go from full torque at zero speed to fast enough to explode the rotor the advantages of cutting edge improvements are limited.
Also an active front end (or some call it an active rectifier module) could be used to dump the regenerated energy from the generating motor in its braking condition as the system would become a regenerative 4 quadrant with the added reverse rectification element. This would also help out with the site harmonics and power correction if the variable frequency drive is large.
Generally, VFD manufacturers do not make filters and vice versa. Now you have a finger pointing situation between manufacturers in the warranty period. A packaged solution always turns out to be the most cost effective solutions there is one point of responsibility if a problem occurs. A properly sized product that is most suitable for the application is always better.
Catch on fly is starting the VFD on a motor that is already rotating. This can happen on a load with high inertia during power outages. You can also experience a reverse turbining effect on a fan which is rotating in reverse direction, here you need to brake, bring speed to zero and then ramp up. You will typically experience this in a Cement Plant on a Cooler Fan. Ideally it should be able to start exactly at the same speed it may be running. Hence it is called catch on fly or flying start.
What is the application? How slow does your customer want to run? What are the existing motors, are they capable of running on a VFD at slower speeds? What is the insulation rating of the current motors? May or may not need new invertor duty motors.
Carrier frequency in fact causes the audible noise. You can diminish the noise with high frequency ripple filters which will add cost to the installation. This may be necessary in places where the public or employees are in close proximity to the SMPS or VFD. In most cases of a VFD you may increase the carrier frequency beyond the audible level of human hearing level, however, not without drawback. The drawback is simply that the VFD now has higher losses in the Power Stack due to higher switching frequencies and may have the need to be de-rated in terms of highest continuous current available.
The reason the VFD manufacturer requires you to use a variable speed drive type motor feeder cable is to reduce the possibility of EMC current caused by the VFD pulsing to escape and not return to the VFD via the cable shield. These currents are at high frequencies in the 500kHz or higher range (radio frequency) and high frequency current only flows in the outer skin of the conductor. If the shield does not have sufficient skin effect, then the impedance will be too high and the EMC current will look for a lower impedance path to return to the VFD through the rest of the plant.
Training now is much more about the specifics of different applications (HVAC, winding etc.) than about the way drives work. I've been training drives for some time, and these days the emphasis is also on interfacing and communications, harmonics, EMC etc. However, many variable frequency drives still give problems because they are incorrectly installed (exposed to dirt and dust) and these basics should be covered as well.
Reducing variable frequency drive parasitic capacitance and bearing currents is a complicated problem with a lot of variables. If you use insulated bearings and don't have a shaft grounding brush things may get worse. The vast majority of 500 hp and smaller motors running on VFDs have no bearing problems. It is more likely to have bearing problems when driving a centrifugal pump where there is a poor ground through the impeller or fluid being pumped.
No easy answer on dv/dt, delta volts/delta time, change in volts/change in time, effect on bearing currents. There is still a lot of research being done on it. As a rule the quicker the voltage rise the more motor problems you may have. But the quicker the voltage raise the less heat loss across the IGBT so the more efficient the VFD, smaller components and heat sink and less cost. One fairly recent way to have it both ways is to have a constantly changing carrier frequency. This makes the fast rise time of the new IGBTs appear to be sloped to the motor. This is more important on the first pulse of each half wave.
Not all variable frequency drives are intended for continuous operation; in some instances, they are simply a "starter" for a rotating machine. In these cases, one VFD may be used to sequentially start several machines - switching each to "bypass" mode once operating voltage and frequency are established, and leaving the machine connected to the supply line for loading/running.
Category
AC Motor Control
Featured

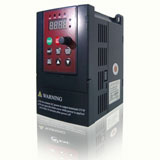
Recent
Increase the speed of a motor by VFD
VFD in Crane and Hoist Applications
VFD for Fire Pump Motors
Is it VFD the best solution to control pump?
3HP VFD, single phase to three phase VFD
Insulated bearings for electric machines
Control ABB VFD through RTD 250ohm directly on water temp
Variable frequency drive Preventive Maintenance
Large VFD trips with power supply by transformer
Induction motor power factor
Understanding VFD basics
Does the motor lifetime depend on the starts number & frequency?
VFD in Crane and Hoist Applications
VFD for Fire Pump Motors
Is it VFD the best solution to control pump?
3HP VFD, single phase to three phase VFD
Insulated bearings for electric machines
Control ABB VFD through RTD 250ohm directly on water temp
Variable frequency drive Preventive Maintenance
Large VFD trips with power supply by transformer
Induction motor power factor
Understanding VFD basics
Does the motor lifetime depend on the starts number & frequency?