HomeEnergy saving
PLCs later added on older industrial facilities "hickup" all the time because of power related problems like I mentioned earlier above, especially on older buildings with newer VFD ect that have been added over time. Sometimes failure to properly isolate analog sensor wiring in conduits and even the controls themselves (plastic wireways) may result in a false input triggering, especially with modifications here and there. One output may result in triggering another falsely.
If the application instead is running on a variable speed and with a changing load then there is also energy to be saved by using a variable frequency drive. There is a lot of literature on this subject. The most saving is due to the variable speed. This is common knowledge and has not anything to do with the Brand or model, but purely that the V/F control is used to control the speed of the motor.
The purpose of using VFD solution is to optimize the energy saving and efficiency of the entire solution. The objective also to optimize the torque requirement at maximum point at any speed range.
At some point the motor has to be disconnected from the variable frequency drive. Usually the motor is equipped with fuses and a contactor, but in very large systems like the amount of kinetic energy stored in the load and all the magnetic energy stored in the motor amount to a fabulous total that somehow has to be dissipated. If you just open the circuit there is going to be arcing and all sorts of collateral damage. To eliminate the need for any maneuvering or protection devices between the VFD and the motor I've been trying to use VFDs rated for motor protection, but those are far less common and on the expensive side.
Regarding active filters, one variable frequency drive or several does not really matter. In general the active filter is sized about 1/3 of the VFD. Thus, if it is a small drive the corresponding active filter might be too expensive compared to AFE or other alternatives. As the installation grows however, the economy of using active filters will improve significantly.
I suggest to use a 6 pulse drive and use a harmonic device as an adder. In today's world the variable frequency drive faces many potential problems. Power failures, lighting strikes, shorts, etc. If a VFD fails for any reason, a replacement VFD can be had at any local distributor within hours. If need be one could buy a different manufacturer's variable speed drive if the application is critical.
Motor like sine voltage/current, but inverter will prefer lower switching frequency. We tested on some small BL motor (<500W). For most load range, the overall system efficiency between these two control methods is similar.
The 6 step control is heavily related to the advanced angle, if there is an easy way to adjust the advanced angle dynamically like the DQ control, 6 step would probably provide an ever higher system efficiency.
I do prefer to use a vfd with DC injection braking or dc-hold functionality, but if you're stuck with "across-the-line" controls, all you need is a few aux contacts on your primary starter, a variable time delay relay, a two pole contactor (preferably with at least one aux contact), and a single phase rectifier (or four appropriately sized diodes.)
With EtherNet and other connectivity capability, Drive Control from PLC's PAC's and DCS's is a normal mode of connection, control, management and monitoring. You can send all of your Data down one cable and receive the data you seek through the same cable. You can back that up with Analog and Digital signals from the PLC to the same variable frequency drive, the options are quite simply endless.
Most of what we do is larger horsepower.. and we have done some single phase input drives in applications up to 350 HP (its rare).. so you may be correct in not needing more capacitors at 1 HP.. we seldom do anything in that range.. However, in larger HP's, the capacitor ripple is an issue.. it heats the capacitors.. its not uncommon to open a single phase input drive and find capacitor goop all over the bottom of the cabinet.
Few manufacturers provide any kind of a transition system in LV VFD bypass systems. Not common. They are almost universally manual (at least in the US) and are used as a backup, ie. emergency operation. Granted, I have seen and sold automatic systems where if the VFD fails the motor is automatically put across the line for continued operation. I always tried to talk my customers out of that option.
* Popularity of SRDS in the past was due to lower capital cost
* Use of SRDS has decreased markedly since the late 1980s due to:
- VFD alternative becoming more and more cost effective
- Operational limitations and significantly higher maintenance of SRDS compared to VFD alternative
- Diminishing difference in equipment cost between SRDS and VFD alternative.
* Use of SRDS has decreased markedly since the late 1980s due to:
- VFD alternative becoming more and more cost effective
- Operational limitations and significantly higher maintenance of SRDS compared to VFD alternative
- Diminishing difference in equipment cost between SRDS and VFD alternative.
Category
AC Motor Control
Featured

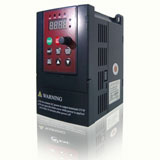
Recent
Increase the speed of a motor by VFD
VFD in Crane and Hoist Applications
VFD for Fire Pump Motors
Is it VFD the best solution to control pump?
3HP VFD, single phase to three phase VFD
Insulated bearings for electric machines
Control ABB VFD through RTD 250ohm directly on water temp
Variable frequency drive Preventive Maintenance
Large VFD trips with power supply by transformer
Induction motor power factor
Understanding VFD basics
Does the motor lifetime depend on the starts number & frequency?
VFD in Crane and Hoist Applications
VFD for Fire Pump Motors
Is it VFD the best solution to control pump?
3HP VFD, single phase to three phase VFD
Insulated bearings for electric machines
Control ABB VFD through RTD 250ohm directly on water temp
Variable frequency drive Preventive Maintenance
Large VFD trips with power supply by transformer
Induction motor power factor
Understanding VFD basics
Does the motor lifetime depend on the starts number & frequency?